金属切削技术和生产经济性=最大输出
2014-7-13 来源:数控机床市场网 作者:-
如果加工工艺可以描绘成一种恒定不变的模型,那么金属切削技术的新发展就能够产生最大的经济效益。从综合或全局的生产经济性角度来看,这对比较不同的可行技术方案具有极为重要的意义。全局生产经济性的定义是:“确保加工工艺的最大安全性和可预测性,同时保持最高的生产率和最低的生产成本。”在对单个加工进行详细的 1:1 优化之前,必须从宏观角度对工艺生产率和成本效益的总体情况进行平衡和优化。采取这一步骤后,可以通过仔细调查适合进行 1:1 优化的情形来实现进一步的改善。
微观和宏观模型
为了实现最佳金属切削结果,传统方法采用一种狭义的微观模型,它基于在一次加工中对单个刀具进行 1:1 优化的情形。而另一方面,宏观模型考虑的是广义上的制造。在这些宏观或全局模型中,生产特定工件所需的总时间具有更具决定性的作用。
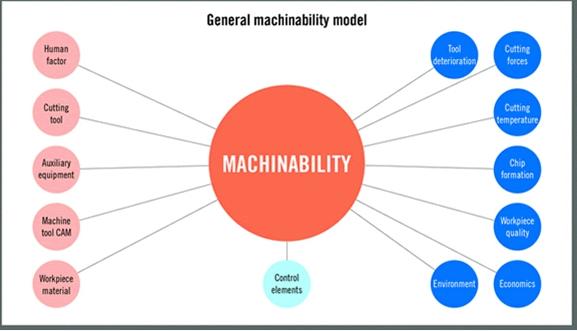
全局优化的一个简单示例是在流水生产线中利用两台机床生产部件。如果无法对机床“B”进行同样的改进,对机床“A”进行的切削时间优化和产量增加就毫无用处。机床“A”增加的产量只会造成机床“B”上等待加工的半成品工件的库存增大,导致额外的成本。在本例中,更好的做法是优化机床 A 上的切削成本。这样做可能会限制机床 A 的生产率,但会降低总成本,同时保持产量。
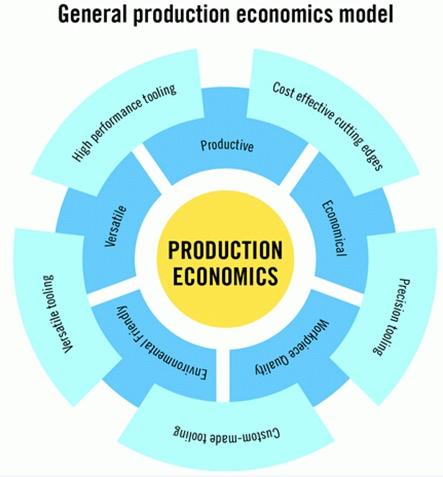
另一方面,在机床 B 等待加工机床 A 生产出的零件时,增加机床 A 的产量将会提高总产量。这在很大程度上取决于车间对其生产加工的组织方式:是采用生产线加工、按批次加工,还是并行加工。虽然无法概括各种情况,但这些示例都表明需要从全局角度出发,同时说明了需要非常细致地开展微观模型优化。
从全局角度出发的要求可适用于机床本身。典型情况可能是一个车间一周 40 小时满负荷运行铣床,它决定将其替换为高速机床。当新机床开始投入运营时,却有一半的时间都处于闲置状态。这使该车间面临寻找新作业以使新机床保持运行的挑战,因此还要支付额外的费用,同时要证明这笔投资的合理性。更好的方法是首先对全局情况进行审视,并预估新机床的更大产量会产生什么结果。
优化切削时间与切削成本
1:1 优化关注的是一个应用场合和单个刀具,旨在以尽可能最低的成本产生高金属切除率。该工艺涉及选择最适用于加工零件的刀具以及采用可行的最大切削深度和最高进给率。当然,最大切削深度和进给率会受到机床功率和扭矩、工件夹紧稳定性和刀具夹紧安全性的影响。
1:1 优化的最后一步是选择最低成本或最大生产率方面的适当标准,并利用切削速度进一步优化该标准的实现。重要的是记住用于决定刀具寿命的 Taylor 模型。该模型证明,对于给定的切削深度和进给量组合,在刀具损耗仍是安全、可预测并且可控制的情况下存在最佳的切削速度范围。在该范围内作业时,有可能对切削速度、刀具磨损和刀具寿命之间的关系进行定性和量化。
起初,随切削速度的增加,加工时间减少且生产率提高。但在增加到某一特定速度后,成本再次开始升高。超过特定的切削速度后,刀具寿命开始缩短,以至于需要频繁更换切削刃。从全局来看,加工时间成本降低所产生的影响要小于刀具成本快速增加所产生的影响。因此,刀具存在某个切削速度,可使两个成本总和得以平衡,从而获得最低总成本。
在追求生产率时,车间必须谨慎,不要过度关注生产细节而未充分考虑全局,即用于生产工件的总工序时间。
质量和生产率:充足但不多余
如今,人们对零件质量水平的要求比过去更加严格。然而,实现最高质量水平有时会显得过犹不及。高质量固然很好,但过高的质量却会浪费资金。总结这一情况的简单理论问题就是:“我们如何生产出功能合格的最差工件?”通过仅满足这个最低要求,成本可以大大降低,生产率也可以显著提高。
同样,如果只关注在较短周期内实现最高的生产率,则金属加工工艺的可靠性就会降低。当在可行性不高的情况下进行连续加工并且超出该限制时,代价就是工件不合格或报废并且损失时间。
质量、生产时间和成本
生产效率包括三个因素:质量、生产时间和成本。此外,还必须考虑能耗、磨损刀具的处置或回收、加工废物等环境因素,以及有关员工健康的安全因素。
很多个体技术因素会影响生产效率。对于金属切削工艺,有 50 - 70 个个体因素会影响效率,而且常常有一个或多个因素会对效率产生明显的影响。典型因素包括刀具/刀具系统、工件配置和材料、设备加工能力和参数、人力因素、外部设备和维护问题。
其中一个最大的影响因素便是刀具和工件相互作用的结果。了解刀具磨损和失效模式对控制金属切削工艺而言至关重要。磨损迹象通常是逐渐发生并且可以预测的,而其他失效模式,如刀具断裂,则缺乏必要的可预测性,因此无法维持可靠的切削工艺。
通用刀具
出于平衡生产率、可靠性和刀具成本的考虑,需要使用可在广泛应用领域内提供通用性和灵活性的刀具。另外,多用途或通用刀具 (see sidebar below) 还满足了制造业明显向更小批量发展的趋势。向更小加工批量的转变源于人们越来越多地运用准时化的生产策略和外包的增加。
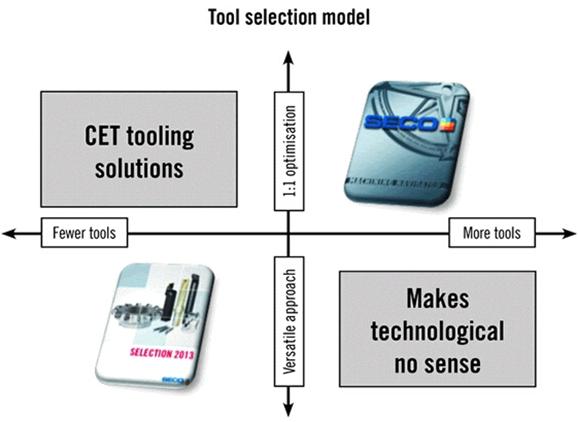
目前,分包商需要定期但并非连续生产小批次的工件。在过去,自动换刀装置有助于减少换刀造成的停机时间,而随着夹具更换装置的使用,则减少了工件操控造成的停机时间。通用刀具可以缩短在工件更换时装入新刀具的时间,并且消除设置和测试新刀具的需要,因此缩短了停机时间。另外,由于车间中不同刀具的数量减少,因此也缩短了刀具处理时间,并增加了加工操作的时间。
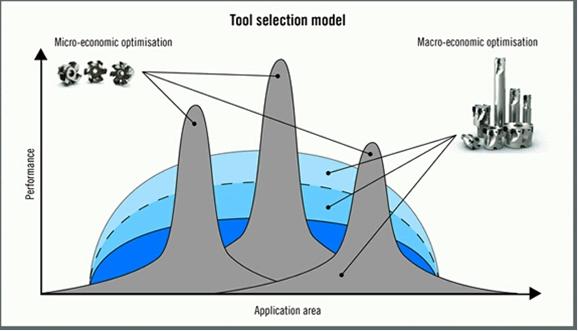
传统的刀具选择策略倾向于以应用为出发点:例如寻找专门用于钢件、不锈钢的刀具,或者用于粗加工或铣削应用的刀具。而比为单一加工选择刀具更重要的是如何使该加工符合全局要求。这种选择应倾向于从生产率、成本效益或可靠性角度来看需要哪种刀具,以及哪种刀具最适合于整个生产工艺。
简单的解决方案
从全局的角度进行工艺优化并不一定很复杂,它可以采用一些非常基本和简单的操作及分析。对使用过的刀具进行检验就是一个重要的例子。正确理解刀具所展现出来的情况能够全面认识车间中进行的工作。例如,如果车间一般采用切削刃为 12 mm 长的刀片,而刀具上的磨损形式仅达到 2 mm 或 2.5 mm,那么该车间所使用的刀片对于所进行的工作来说可能过大。使用切削刃为 6 mm 的刀具应该就绰绰有余,而切削刃 6 mm 长的刀具比切削刃 10 mm 长的刀具要便宜得多。这种简单的观察可在不降低生产率的情况下减少 50% 的刀具成本。
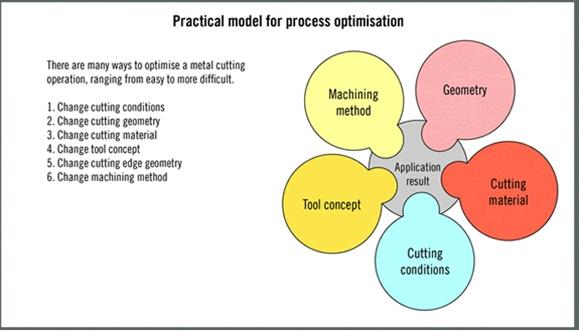
刀具制造商的回应
今天,刀具制造商认识到客户越来越青睐那些生产率高且经济实惠的通用刀具系统,并对此作出了积极的回应。新开发的通用刀具在提高产量的同时还降低了刀具库存、刀具操控、重新对刀和测试成本。
此类刀具的一个示例是山高的 Turbo 铣刀系列。这些刀具在广泛的应用中具有卓越的通用性和灵活性,可以提供出色的成本效益和高性能。它们旨在提供无差错的生产和高质量的工件表面粗糙度。这些刀具具有正向切削槽型,可降低功耗、延长刀具寿命并尽可能增加切削深度和进给率。这些刀具的能力代表了迈向总体优化工艺的第一步。
通用刀具的另一方法是装配一套适用于各种应用的刀具。山高精选刀具专为提供灵活性而设计。所选的刀具组包括有限数量的刀具,它们可能未必提供绝对的最大生产率或成本效益,但在加工日益变化的各种工件和部件所需的最大灵活性方面,它们却是最经济的最佳选择。
本质上,这种方法并不适合各种需求。例如,与之相对的便是高度专业化的产品,如 PCBN 刀具,专门用于对特定的工件材料进行极高质量和/或极高生产率的加工。PCBN 刀具非常昂贵,但却是某些专业应用的最佳选择。
从批量的另一方面来看,定制工程刀具 (CET) 是一种专为特殊应用的大批量生产而定制的方法。该刀具旨在限制对不同刀具的库存要求,但仍有可能实现微观和宏观优化。
正如制造车间必须从整个生产工艺的全局角度出发来选择金属切削技术,刀具制造商必须开发能够满足广泛客户需求的产品系列。
投稿箱:
如果您有机床行业、企业相关新闻稿件发表,或进行资讯合作,欢迎联系本网编辑部, 邮箱:skjcsc@vip.sina.com
如果您有机床行业、企业相关新闻稿件发表,或进行资讯合作,欢迎联系本网编辑部, 邮箱:skjcsc@vip.sina.com