GF加工方案助Lotus F1车队效率提升
2014-3-26 来源:数控机床市场网 作者:
为了大力提高生产率和加工性能, Lotus F1车队近期投资购置了六台均集成有GF加工方案自动化性能的新型五轴铣削加工中心。
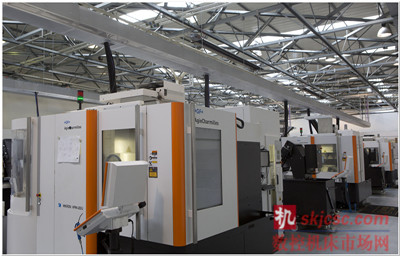
这六台新型的MIKRON HPM450U铣削加工中心,已在Lotus F1车队位于英格兰恩斯通的总部安装投产,同时也成为了英国一级方程式车队全面现代化生产设施的核心。在运行半年以后,Lotus F1车队的首席营运官(COO)Thomas Mayer先生非常满意机床运营情况:“当初我们做出了使我们的铣削能力扩展到五轴的战略决策,这样的决策帮助我们选择的系统,能够在一次装夹过程中完成整体工件的加工。从而使我们的生产效率大大增强,有效提高了我们的机床利用率,并实现了更高和更一致的部件精度,同时极大地降低了单位成本。”
在投资MIKRON HPM 450U之前,Lotus F1车队主要依赖于三轴铣床加工高精密的复杂零件。虽然也获得不错的效果,但出于对生产率的考虑他们因此另有期望。同时三轴铣床一个最大的缺点就是在机床上的调试设置时间过长。“我们期望自己能更加高效,”Mayer解释说。“在使用旧的三轴机床铣削加工过程中,需要浪费太多的时间进行机床的设置以及各个辅助装置的规划和设计。最重要的是,在生产过程中频繁出现的中断现象,不仅对生产率有负面影响,而且在工件进行必要的手动处理时,对工件的精度也有影响。我们知道,五轴机床将是满足我们生产要求的最理想的解决方案,对于高精密、复杂零件的小批量生产而言,如果我们能够在一次装夹过程中完成工件加工,产量有可能有相当大的提高。”因此Lotus F1车队决定用六台新的五轴机床取代原有的三轴机床。
机床的选择
“因为我们希望用新的五轴机床进行标准化生产,因此机床必须是相同的,”Mayer说。这些标准化生产的目标,不仅需要相同的机床,而且也需要相应相同的配套刀具、夹紧装置等。Thomas Mayer说:“我们希望机床具有最大的灵活性和100%的兼容性。在一台机床出现状况的情况下,我们必须能够迅速、无缝地切换到另外一台上。这样一个统一的采购方式也可以让我们的编程和操作人员在同一时间熟悉所有的新机床。”
一旦达成了机床更新换代的决定之后,Lotus F1车队就开始着手寻找最理想的机型,并为此制订了一个主要要求清单。这些要求包括机床外形尺寸(占地面积)、加工能力、性能特点(特别强调自动化集成)、可用性和机床成本,以及需要的维护次数。最后一点也是很重要的一点,就是在英国的GF加工方案的客户服务部门的质量和速度对Lotus F1车队来说是一个关键因素。“HPM450U机床从一开始就满足我们最大的期望,”Thomas Mayer总结说。“因此,通过只需一次装夹过程完成工件加工,我们已大大提高了我们的工作效率和质量。”
MIKRON HPM 450U
GF加工方案的MIKRON HPM 450U 完全满足Lotus的所有要求。高性能、结构紧凑和具极高性价比的五轴铣床,配置直驱式旋转倾斜式工作台,并通过三加二定位和五轴联动加工,执行标准的铣削和钻削加工工艺。高性能主轴(30kW,20,000 rpm)和自动化集成(带7工位托盘交换装置和120个刀位的换刀装置)更好地确保了优异的加工性能。一系列高效SMART智能加工模块,在二十四小时运行过程中能够确保最高的生产率和生产的高度灵活性,以及铣削过程的可靠性而成为机床另一大优势。由于MIKRON HPM450U的多功能性,其可加工的材料范围非常广泛,非常适合例如铝、钢、不锈钢的加工,以及难以加工的硬质材料。
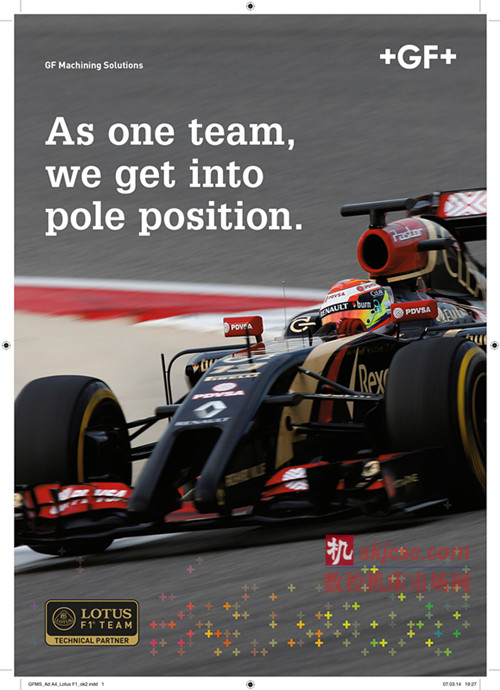
投稿箱:
如果您有机床行业、企业相关新闻稿件发表,或进行资讯合作,欢迎联系本网编辑部, 邮箱:skjcsc@vip.sina.com
如果您有机床行业、企业相关新闻稿件发表,或进行资讯合作,欢迎联系本网编辑部, 邮箱:skjcsc@vip.sina.com
更多相关信息