碳纤维复合材料手工制孔刀具和工具的选择方案
2014-1-24 来源:数控机床市场网 作者:罗海勇 郑伟 涂卿
[摘要 ] 目前,碳纤维复合材料正广泛应用于飞机制造,而装配中制孔是重要的一环,因此,选择合适的刀具和工具是保证制孔质量的前提。国内各公司采用的工具和刀具各不相同,为提高复合材料的制孔技术,应从众多实际应用实例中总结出更优的选择方案。
关键词: 刀具 工具 选择方案 碳纤维复合材料
现今生产中用途广泛的复合材料主要分为玻璃纤维复合材料和碳纤维复合材料,而碳纤维复合材料所具有的高强度、高刚度、抗疲劳性能好、耐高温性好等优点,使其在飞机设计、制造上具有更好的优势和应用。随着碳纤维的广泛应用,随之也带来了碳纤维复合材料在加工和装配上的问题。此时,碳纤维复合材料的缺点更加的凸显出来,成为了钻孔、装配的主要问题来源。在碳纤维复合材料钻孔时主要克服碳纤维复合材料结构的高强度、高硬度、导热性差、各向异性、层间强度低等难题。同时,在钻孔的过程中也极易出现材料烧伤、毛刺、分层、撕裂等缺陷,别是刀头出口端更容易引起撕裂等现象(图 1) 。
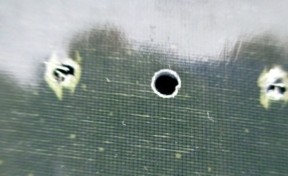
图1 刀头出口端撕裂
在无法进行重新修复的情况下可能导致部件的报废,造成重大的损失。
1 碳纤维复合材料的加工问题的提出
当前,国内外通用飞机越来越多地采用复合材料,特别是在轻型通用飞机上的应用更加广泛。公司目前所研制的轻型飞机也采用全碳纤维复合材料结构,飞机的机翼(包括翼梁、桁条和蒙皮)、机身、尾翼、蒙皮、油箱、发动机舱都是采用复合材料。同时,在低成本化的指导下,采用更经济的加工、装配工艺成了必须的选择。因此,如何协调解决好碳纤维复合材料的制孔和装配问题,是提高生产效率和降低生产成本的关键所在,也是提高飞机制造质量必需要解决好的问题。
2 碳纤维复合材料手工制孔工艺技术
目前,在碳纤维复合材料手工制孔中,主要需解决刀具类型和工具类型的选择。
2. 1 钻孔前的准备
钻孔前,在有条件的情况下,都需要在刀头出口端贴上铝基胶带或顶上木块,这样也可以有效地避免出口劈裂。
2. 2 刀具棒料和涂层的选择
针对碳纤维复合材料在加工中表现出的高硬度、导热性能差等特点,刀具的材质应选用硬质合金棒料,表面采用气相沉积金刚石镀膜 (CV D)或聚晶金刚石镀膜(PCD)涂层。经过制孔试验表明,采用 2700r/m in 的CP7300 气钻钻制 4m m 厚的板材时,带涂层的硬质合金钻头可以钻制 50~60 个孔,在出现进给困难后,通过利用砂轮磨削刃口后, 可继续钻制 15~20 个孔。而普通的高速钢 (H SD) 刀具则基本无法完成制孔,其刀头在复合材料制件的表面上出现打滑现象,其刀具本身也容易出现烧伤。
2. 3 刀具刃型的选择
目前,复合材料制孔采用的刀具主要分为匕首钻、麻花钻和金刚砂涂层扩孔锯。
2. 3. 1 匕首钻
采用钻、绞一体化设计,进给工作的刀头的型式大致相同,排屑部分有的采用直刃,国内代表为厦门金鹭公司的直刃上首钻(图 2),也有采用螺旋刃的,国外代表公司为Sandvik。当采用匕首钻配合 CP7300 手动气钻进行手工制孔时,其制取的孔壁、刀头进口端及出口端的质量良好,能满足工艺要求,同时也基本能保证质量的稳定性。
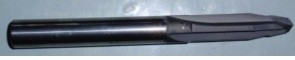
图2 直刃匕首钻
此类匕首钻螺旋角为 90,在钻尖处没有横刃存在,刀具与材料接触面积小,钻孔过程中所产生的热量少,能够有效避免材料烧伤现象。但其排屑槽为直槽,不能有效排出金属切屑,仅适用于纯复合材料夹层上的钻孔,并不适合于复合材料与金属材料夹层。对于直径φ>14m m 的孔也不适合采用匕首钻,特别是钻制厚度H<3m m 的薄板时,匕首钻的刀头长度超过板厚,刀具直径过大,给予板材的横向力比较大,造成钻出的孔成梅花形或五角星形,建议钻制直径φ>14m m 的孔时采用金刚砂涂层扩孔锯(图 3)。
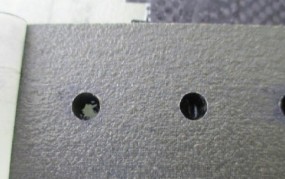
图3 匕首钻制孔效果
2. 3. 2 麻花钻
采用倪志福式多刃刀头的麻花钻在制取 3m m 以下碳纤维板材时,其制孔质量良好,进行的孔不易出现梅花形,圆度好。在对 3m m 以上厚的板材进行的制孔试验中,其制孔质量无法保证,其刀具刃口特别锋利,容易造成磨损,当钻制金属与复合材料夹层板时,更容易造成崩刃(图 4)。
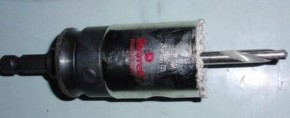
图4 金刚砂涂层扩孔锯
2. 3. 3 金刚砂涂层扩孔锯
当钻孔直径φ>14m m 时,同时孔的精度为自由公差时,可采用金刚砂涂层扩孔锯,金刚砂涂层扩孔锯能很好地克服碳纤维复合材料的高硬度的特点。试刀试验表明,当用 900r/m in 钻配合φ43m m 扩孔锯进行钻削时,能顺利地切入板材进行钻削,在钻孔完成后,测得其孔径为φ42. 90m m ,同时其孔壁质量良好,满足工艺要求。
需要注意的是,当使用扩孔锯进行制孔时,通常钻制的孔径比较大。产生的切削阻力也更大,需要提供的进给力比较大,当钻制的板材厚度 H>10m m 时,人工钻制比较困难,因此,可以采用下文中推荐的自动进给钻来制孔。
3 工具的选择
手工制孔时,对于直径小于 14m m 的孔,一般采用的是匕首钻配合铰刀来完成,为了确定选择工具的转速的合理范围,分别做了如下几个对比试验。
3. 1 试验方案如下
A :20000r/m in 气钻,φ3m m 硬质合金匕首钻,3m m厚单向带 / 10m m 厚编织带;
B :6000r/m in 气钻,φ3m m 硬质合金匕首钻,3m m厚单向带 / 10m m 厚编织带;
C :6000r/m in 气钻,φ6. 35m m 匕首钻,6m m 厚单向带,1 层 / 3 层铝基胶带;
D :900r/m in 或 3200r/m in 气钻,金刚砂涂层孔锯φ43m m ,13m m 编织带。
3. 2 试验结果分析
当采用 A 组合试验时,由于转速过高,稳定性差,特别在钻削 3m m 以下薄板时,工人来不及调整钻头位置,容易造成偏移,致使孔径过大,超过理论要求。而在钻削 10m m 厚的编织带板材时,由于板太厚、手工垂直度不够、转速太快,从而发生了刀具断裂现象。
当采用B组合试验时,由于工具转速低于6000r/m in 时 (可通过调节进气量),手持气钻能获得较好的稳定性,孔的加工效果较好,孔壁、孔径都满足工艺要求,初步说明在采用手动工具加工时宜采用转速不高的气钻。
当采用 C 组合试验时, 在出口端贴上 3 层铝基胶带时比贴 1 层铝基胶带制孔的出口端质量好,可以看出在出口端贴胶带能起到比较好的保护效果。
当采用 D 组合时,此试验采用同一种孔锯,用不同转速气钻进行钻削。当使用 3200r/ m i n 的气钻进行钻削时,由于钻削的直径比较大,孔锯在板材表面产生打滑,不利于切屑。在未贴铝基胶带时出刀口质量不好,存在劈裂现象。而当使用 900r/ m i n 气钻进行钻削时,能顺利地切入板材进行钻削。但是由于板材很厚,当切削进入6m m 深时,钻削阻力非常大,钻削很费力、费时,同时,散热也极其不好,容易烧伤材料。由于试验时,精度未重点考虑,利用扩孔锯的引导杆从反面钻削,可以使钻削省力很多。当精度要求高时,由于手动气钻不稳定,建议采用自动进给钻加工(图 5,图 6),其液压装置能精确控制进给速度,从而能保证稳定性,提高钻孔效率。
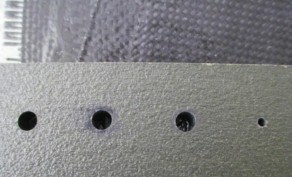
图5 C 组合制孔试验板
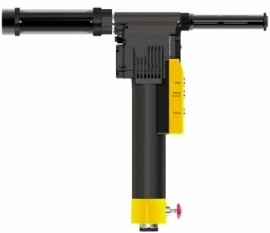
图6 自动进给钻
4 辅助工具及材料的选择
4. 1 便携式垂直套
在用手工气钻钻孔时,由于人工手持时通过自己肉眼判断有误差,且气钻转动时手会产生不同程度的抖动,再遇上材料夹层厚度较厚时,手工钻孔的垂直度很难保证,钻孔的稳定性进一步降低,将大大增加孔加工缺陷的产生。因此,在有条件的情况下,手工钻孔应使用便携式垂直器钻孔,以起到稳定刀具的作用,从而增加钻孔过程中的稳定性。
4. 2 钻孔出口垫板
刀头出口端是最容易产生缺陷,如撕裂、分层、毛边等缺陷的位置。在刀头出口端贴上几层铝基胶带,然后用平头木块、夹布胶木或铝板等顶住出口端,可有效减少出口端孔缺陷的产生。
5 结束语
随着碳纤维复合材料的广泛应用,其制孔技术也在逐步提升,本文是基于目前飞机生产过程中所采用的方法作了如下初步的结论:
(1)碳纤维复合材料制孔尽量采用硬质合金或带金刚石涂层的(常见为气相沉积金刚石镀膜(CV D)或聚晶金刚石镀膜(PCD)硬质合金刀具) ;
(2)刀具钻孔时的转速和进给:小直径孔选择中转速工具和较大进给量,大孔选择低转速工具和降低进给量,气钻转速优先选择 2000~6000r/ m i n;
(3)在碳纤维复合材料薄板(3m m 以下)上制孔时,宜采用更锋利的倪志福式多刃刀头的硬质合金麻花钻;
(4)在碳纤维复合材料板材制取超过φ14mm 的孔时建议采用金刚砂涂层孔锯。气钻转速低于 3200r / mi n;
(5)在每次钻孔时均需在出刀位置贴上铝基胶带,出口端用铝块、夹布胶木等顶住。
提高复合材料制孔技术的水平,对于提高飞机复合材料制造质量和企业生产效率有明显的成效,对加快和促进复合材料在国内航空制造业的应用具有重要推动作用。
投稿箱:
如果您有机床行业、企业相关新闻稿件发表,或进行资讯合作,欢迎联系本网编辑部, 邮箱:skjcsc@vip.sina.com
如果您有机床行业、企业相关新闻稿件发表,或进行资讯合作,欢迎联系本网编辑部, 邮箱:skjcsc@vip.sina.com